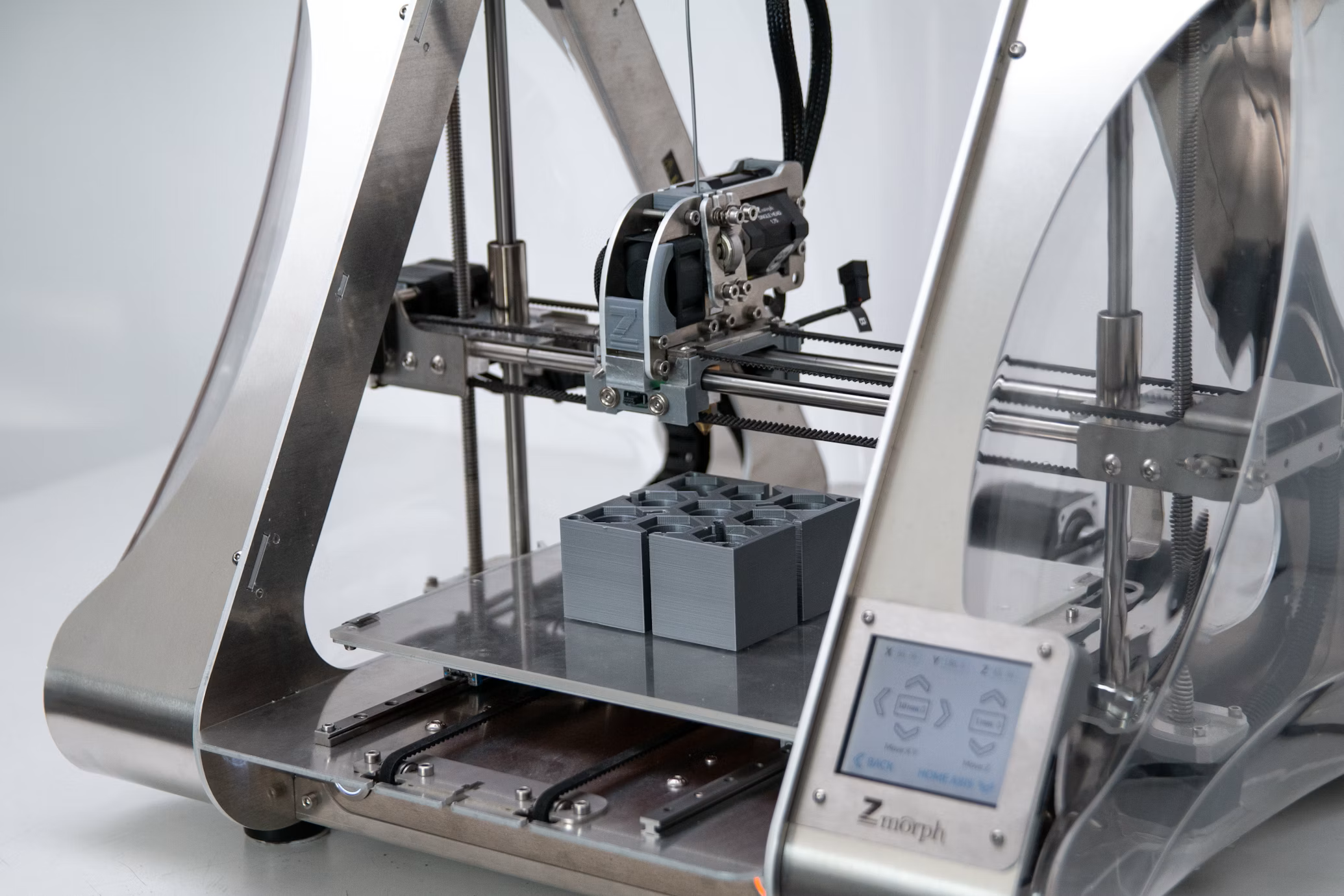
Have you ever wanted to create custom molds but got stuck with limitations in traditional methods? Don't worry, we have the solution: 3D printing will change the game. Whether you're a hobbyist experimenting with new materials, an engineer prototyping designs, or a small manufacturer looking for cost-effective solutions, understanding 3D printed molds will open new doors of opportunity.
From resin and silicone casting to working with concrete and even injection molding, 3D printing allows you to design and create intricate, diverse molds without the high costs of traditional mold-making methods.
In this guide, you will learn what types of molds you can print, which materials to choose for strength and detail, and all the essential knowledge about 3D print mold making. Let’s dive in!
Types of 3D-Printed Molds
Let’s start with 3D printed molds for casting — this is an excellent place to begin. Have you ever wanted to create custom parts, figures, or architectural details? 3D printed molds allow you to pour liquid materials like resin, silicone, or concrete into a cavity that hardens, becoming a solid shape.
So, what makes 3D printing so powerful in mold-making? It’s the ability to create complex, highly customized molds without the constraints of traditional manufacturing.
For example, if you're developing a unique resin jewelry piece — maybe a pendant with intricate details that are hard to carve by hand. Instead of manually cutting a silicone mold, you can 3D print the mold to ensure precision and repeatability.
Common Types of Casting Molds
3D Printed Molds for Casting
Ideal for resin, wax, and even metal casting using lost-wax techniques. Many hobbyists and small businesses use them for custom jewelry, tabletop miniatures, and artistic resin pours.
3D Printed Silicone Molds
Frequently used for creating flexible molds, great for soap making, candle pouring, or food-safe molds like chocolate molds.
3D Printed Concrete Molds
Popular in architecture and home décor, these molds allow you to create custom planters, tiles, and decorative sculptures.
3D Printed Resin Molds
Best for intricate, small projects where fine detail is essential, such as custom keycaps for mechanical keyboards or detailed model parts.
3D Printed Injection Molds
Injection molding is widely used in manufacturing, but the cost of traditional metal molds can be prohibitively high for small projects or prototyping. Why spend a fortune when you can use 3D printed injection molds? These offer a more economical alternative for low-volume plastic part production.
Engineers working on a new electronic gadget may need a small batch of custom plastic housings. Instead of spending thousands on CNC-machined molds, they can print a 3D mold and inject thermoplastics like ABS or PETG to test their design before full-scale production.
Key Considerations for 3D-Printed Injection Molds
-
Material Choice Matters: Regular PLA won’t withstand the heat and pressure of molten plastic. High-temperature SLA resins, glass-filled nylon, or reinforced filaments work best.
-
Design for Durability: Unlike metal molds, 3D printed molds may wear out faster, so reinforcement and cooling channels are often needed.
These are excellent for prototyping and small production runs. Although unsuitable for mass production, they work great for testing product designs.
3D Printed Carbon Fiber and Epoxy Molds
For those working in high-performance industries like aerospace, automotive, or sporting equipment manufacturing, 3D printed molds made from carbon fiber and epoxy resin offer exciting possibilities.
Carbon fiber molds make lightweight, high-strength components like drone frames, car parts, and even bicycles. Traditional carbon fiber molding requires expensive, labor-intensive hand-laying techniques. With 3D printing, you can create custom molds faster and more affordably.
Epoxy resin molds are perfect for artistic applications like river tables, custom furniture, and decorative resin pours. Instead of handcrafting wooden molds, creators can 3D print intricate designs and cover them with a release agent for a smooth result.
Knowing how to select the right mold type for your project expands the potential of 3D printing. Whether casting resin jewelry, prototyping plastic parts, or creating carbon fiber components, 3D printed molds bring innovation and efficiency.
How to Create a 3D-Printed Mold
A 3D printed mold is a combination of:
-
Design
-
Material selection
-
Post-processing methods
Whether you're making a simple silicone mold for resin casting or an injection mold for low-volume plastic production, following the correct steps is key to ensuring durability and high-quality results.
How to Design a Mold?
If your goal is to create a final product that comes out smoothly and functions well, you need to focus not only on making the cavity in your CAD software but also on planning. Here are some steps to do it correctly:
-
Use CAD Software
Tools like Fusion 360, Blender, and Tinkercad allow you to create precise mold designs. If you’re designing a complex part, parametric modeling in Fusion 360 helps you easily adjust dimensions.
-
Consider Draft Angles and Parting Lines
Have you ever noticed how ice cubes easily pop out of a tray? That’s due to draft angles — slight slants in the mold walls that help release the cast part. The part might get stuck without them, requiring forceful removal that could damage the mold and the final product.
-
Add Alignment Pins for Multi-Part Molds
If your mold consists of two or more parts, alignment pins or keys will help keep everything in place during assembly. This ensures that every cast comes out clean and intact, which is especially important for projects like resin jewelry or injection-molded prototypes.
Let’s Consider a Practical Example
Imagine you're designing a mold for mechanical keyboards. Without proper alignment pins, the two halves of your mold might shift during curing, leaving a visible seam on the finished product. Adding small round alignment pins could solve this issue.
Choosing the Right 3D Printing Technology
Not all 3D printing methods are the same, especially in mold-making. The best choice depends on your required level of detail, durability, and intended application.
Technology |
Best For |
FDM (Fused Deposition Modeling) |
Large and durable molds, ideal for silicone and concrete casting (PLA, PETG, ABS) |
SLA (Stereolithography) |
High-detail, smooth surface molds, great for resin casting and small-scale injection molding (Resins) |
SLS (Selective Laser Sintering) |
Industrial-grade molds with excellent durability and heat resistance (Nylon) |
A Closer Look at Each
-
FDM is great for beginners
If you’re making a mold for silicone casting, printing in PETG or ABS with a high filler percentage (70-100%) ensures durability. However, FDM prints often require post-processing (sanding, sealing) to achieve smoother results.
-
SLA is best for complex designs
Need super-fine details for jewelry molds? SLA printing using high-temperature resins delivers a glossy, high-precision finish with minimal post-processing.
-
SLS for professional
SLS printing using nylon provides outstanding strength and heat resistance if you need molds for high-temperature materials or industrial applications.
A small business owner making resin stands might use FDM printing with PETG for strength, while a jeweler creating delicate silver pieces might opt for SLA printing to capture intricate details.
With 3D printing, mold-making is more accessible, faster, and cost-effective. Whether casting with resin, silicone, concrete, or plastic, the possibilities are endless when you embrace 3D printed molds.
Printing and Post-Processing
Once your mold is designed and printed, post-processing is crucial for achieving the best results.
Set proper print settings
Use a high infill percentage (50-100%) for strength and print slowly for better layer adhesion.
Sand and polish the printed mold
FDM prints often have visible layer lines, which can leave unwanted textures on cast objects. Wet sanding with fine-grit sandpaper (400-1000 grit) and applying a clear coat or epoxy can create a smoother mold surface.
Apply a release agent or sealant
This prevents materials like resin or concrete from sticking to the mold. PTFE spray, wax, or silicone mold release are commonly used options.
Suppose you’re making a 3D-printed mold for concrete planters. Without a proper sealant, the rough surface of an FDM-printed mold can cause air bubbles and imperfections in the final cast. Coating the mold with epoxy resin or polyurethane ensures a flawless finish.
Best Materials for 3D-Printed Molds
Now, let's get to the most critical part – choosing the right material for your 3D-printed mold, as it will determine the final result. Different materials have unique properties that make them suitable for specific tasks. Here’s an overview of the best options:
Application |
Recommended Material |
Silicone casting |
Standard/Flexible SLA resin |
Concrete molds |
PETG, ABS |
Epoxy resin molds |
Smooth SLA resin, ABS |
Injection molding |
High-temp SLA resins |
Metal casting |
PLA (for lost-PLA casting) |
Let’s dive deeper into why these materials work best and how to get the most out of them.
Silicone Casting
If you’re making silicone molds for resin, candle making, or even food-safe applications, SLA resins are your best bet. Standard SLA resin offers fine details, while flexible SLA resins allow easy de-molding without breaking delicate designs. A great example is using 3D-printed molds to create custom soap bars or intricate resin jewelry.
Concrete Molds
PETG and ABS are excellent choices for making reusable concrete molds. These materials withstand repeated casting cycles and resist cracking. A good example is printing a mold for custom garden stepping stones or decorative tiles. PETG’s flexibility prevents breakage, while ABS protects against wear and tear.
Epoxy Resin Molds
For epoxy resin molds, smooth SLA resins work best due to their high detail and minimal layer lines. A polished SLA mold ensures a flawless finish if you’re crafting river tables, coasters, or artistic resin sculptures. ABS is also a good option if you need a more impact-resistant mold for larger projects.
Injection Molding
Injection molding requires high-temperature SLA resins to withstand the pressure and heat of molten plastic. These specialized resins allow hobbyists and small manufacturers to create short-run plastic parts without the cost of traditional aluminum molds. Imagine 3D-printing a mold
This method makes it possible to produce custom phone cases or small mechanical components.
Metal Casting
For metal casting, PLA is the go-to material for lost-PLA casting. This method involves printing a PLA mold, coating it in a ceramic shell, and then burning out the PLA, leaving a cavity for molten metal. It’s a fantastic way to create custom brass, aluminum, or even silver parts — perfect for crafting jewelry, machine parts, or artistic sculptures.